How to Diagnose Hydraulic Pump Failures Effectively
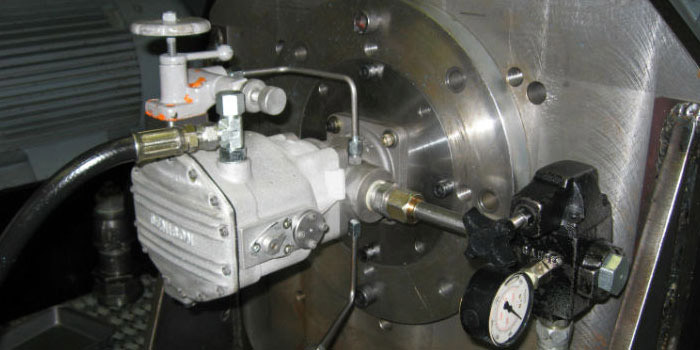
Hydraulic pumps are at the heart of many heavy machines, powering everything from industrial equipment to construction vehicles. When they fail, productivity can come to a screeching halt. Knowing how to diagnose these failures effectively can save you time, money, and a lot of frustration. But where do you start when something goes wrong with your hydraulic pump?
What’s the First Sign of Trouble?
Hydraulic systems don’t just stop working out of the blue. Most failures give you warning signs well before they reach a critical point. Have you noticed unusual noises, sluggish performance, or a drop in pressure? Maybe your equipment is running hotter than usual, or there’s a sudden leak. These are all clues that something’s not right. Paying attention to these early signs can help you avoid more serious issues down the line.
Take noise, for example. A hydraulic pump that whines or growls could be struggling with cavitation or aeration. If you ignore this, it can quickly lead to wear and tear on the pump’s internal components. Similarly, sluggish performance might indicate a restriction in flow or a failing pump. Always trust your instincts—if something feels off, it probably is.
Start With the Basics
Before diving into complex diagnostics, it’s always worth checking the simplest causes first. Is the hydraulic fluid at the correct level? Low fluid can cause a host of problems, including cavitation and overheating. If the level is fine, inspect the fluid itself. Is it clean, or does it look milky or discoloured? Contaminated or degraded hydraulic fluid can wreak havoc on your system. Replacing old or dirty fluid is often a quick and cost-effective fix.
Next, look at the filters. A clogged filter can restrict flow, reducing efficiency and causing strain on the pump. If your filters are overdue for replacement, swap them out and see if the issue improves. These straightforward checks can save you hours of unnecessary troubleshooting.
Digging Deeper: Mechanical Issues
If the basics don’t reveal the problem, it’s time to investigate the pump itself. Start by inspecting for visible damage. Are there cracks, dents, or other signs of wear? External damage could indicate internal issues as well.
Listen closely to the pump while it’s running. Unusual noises—such as banging, rattling, or a high-pitched squeal—often point to internal damage or component failure. For example, a worn-out bearing could cause excessive vibration, while damaged gears might produce grinding noises. If you hear something unusual, stop the system immediately to prevent further damage.
Another key area to check is the seals. Hydraulic pumps rely on tight seals to maintain pressure and prevent leaks. A damaged or worn seal can lead to pressure loss, which reduces performance and efficiency. Replacing faulty seals is a relatively simple repair that can make a big difference.
Pressure Testing: A Vital Step
Pressure testing is one of the most reliable ways to diagnose hydraulic pump failures. Using a pressure gauge, measure the output pressure of the pump under normal operating conditions. Is it lower than the manufacturer’s specifications? If so, you might be dealing with internal wear, such as worn vanes, pistons, or gears.
Pressure testing can also help you identify issues like internal leakage. If pressure builds up slowly or fluctuates, it could mean that fluid is bypassing worn components inside the pump. In this case, a rebuild or replacement might be necessary.
Common Causes of Hydraulic Pump Failures
To fix the problem, it helps to understand why hydraulic pumps fail in the first place. Here are five of the most common causes:
- Contamination – Dirt, water, or other contaminants in the hydraulic fluid can cause abrasion, corrosion, and blockages.
- Overheating – Excess heat can degrade fluid and damage components over time.
- Cavitation – This occurs when air bubbles form in the fluid, causing vibration and damage to the pump’s internals.
- Poor Maintenance – Neglected filters, old fluid, or worn seals can all lead to pump failure.
- Improper Use – Running the pump at the wrong pressure or speed can strain the system, leading to premature wear.
By recognising these causes, you can take steps to prevent similar issues in the future.
Preventing Future Failures
No one wants to deal with a failed hydraulic pump more than once. That’s why preventive maintenance is so important. Regularly checking fluid levels, replacing filters, and inspecting for wear can extend the life of your hydraulic system. Keeping a maintenance log can also help you spot patterns or recurring issues, giving you the chance to address them before they turn into major problems.
If you’re running heavy equipment in demanding environments, it’s worth investing in high-quality hydraulic fluid and filters. These might cost more upfront, but they can save you significant repair costs in the long run. Training your team on proper hydraulic system use and care is another simple but effective way to avoid unnecessary failures.
When to Call an Expert
Sometimes, despite your best efforts, the problem might be too complex to diagnose on your own. That’s when it’s time to bring in a professional. Hydraulic specialists have the tools and expertise to pinpoint issues quickly and accurately, saving you valuable downtime. If you’re unsure about pressure testing, internal diagnostics, or any other aspect of troubleshooting, don’t hesitate to seek help.
Keeping Your Hydraulic Systems Running Smoothly
Diagnosing hydraulic pump failures doesn’t have to be overwhelming. By paying attention to early warning signs, starting with simple checks, and using tools like pressure testing, you can identify and address problems effectively. Remember, most failures stem from preventable issues like contamination, overheating, or poor maintenance. With a proactive approach and regular upkeep, you’ll keep your hydraulic systems running smoothly for years to come. When in doubt, don’t be afraid to reach out to a professional for guidance.