Planning for the Worst: Creating a Cold Room Emergency Response Plan
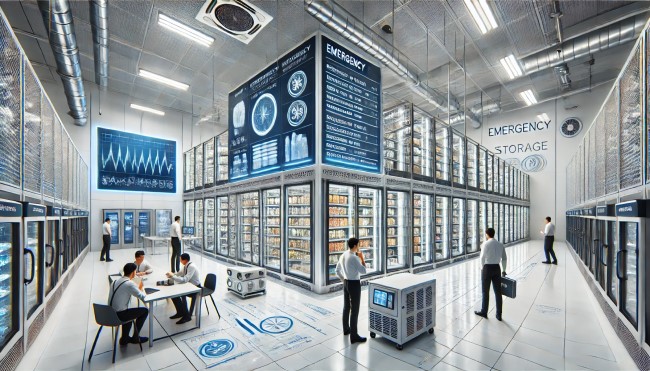
Cold rooms are essential for preserving temperature-sensitive products, from food to pharmaceuticals. When something goes wrong, the impact can be severe—leading to spoiled goods, financial losses, and operational downtime. That’s why having a solid emergency response plan in place is vital. Let’s go through creating a comprehensive cold room emergency response plan, so you can handle emergencies effectively and minimise the risks.
Assess Potential Risks and Vulnerabilities
The first step in creating a cold room emergency response plan is to assess the risks your cold room might face. These could include power outages, equipment failures, and temperature fluctuations. Identifying these potential risks allows you to prioritise which ones need attention first.
Start by listing common risks such as power failure, refrigeration breakdown, door seal damage, water leaks, and condensation. It’s also important to evaluate your current systems, checking if your backup power, alarm systems, and monitoring equipment are up to date and fully functional. Additionally, assess any external risks like natural disasters or extreme weather conditions that could impact your cold room.
Establish Emergency Contacts
In case of an emergency, having the right people to contact is crucial. This includes both internal and external contacts, such as emergency repair services, suppliers, and your team members. Creating a list of emergency contacts should be one of the first things you do. This list should include technicians, emergency services, and key staff members responsible for cold room management.
Make sure to include people who are available outside normal working hours, such as after-hours repair services, and update the contact list regularly to ensure everyone has the correct information. You can hire emergency cold room or fridge freezer by hitting the link.
Develop Temperature Monitoring and Alerts
Monitoring the temperature is one of the most important aspects of cold room management. A sudden temperature shift could jeopardise the quality of your stored goods, so it’s essential to have automated temperature monitoring and alerts in place.
Install a temperature monitoring system that tracks both temperature and humidity levels 24/7. Setting thresholds for temperature fluctuations is crucial; any time the temperature moves outside of these limits, an alert should notify you immediately. Regularly test your system to ensure that alarms will be triggered when necessary, giving you the opportunity to take action before any major damage occurs.
Plan for Power Outages
Power failures can be one of the most devastating events for a cold room. Without power, temperatures can rise quickly, leading to spoilage or damage to goods. It’s essential to have a strategy in place to deal with power outages, especially if they happen unexpectedly.
Invest in a backup power solution such as a generator or battery backup to keep the cold room functioning during a power outage. Testing the backup power system regularly is important to ensure it will work when needed. Additionally, if the outage is prolonged, you should have a contingency plan for transferring perishable goods to an alternative storage location or making arrangements for emergency deliveries of goods.
Create a Temperature Recovery Plan
In the event of a cold room failure, having a plan for recovering the temperature quickly without compromising the integrity of your goods is essential. This plan should focus on how to bring the temperature back to its optimal range as fast as possible.
To do this, establish a rapid cooling protocol that outlines how to re-establish the correct temperature quickly, whether by adjusting refrigeration settings or moving items to a different cold room. Monitor the products closely for any signs of damage, such as thawing or spoilage, and be ready to take action if necessary, such as transferring goods to another storage location or discarding any irreparably damaged items. Make sure your staff is trained on how to execute the recovery plan effectively.
Signs There Could Be Something Wrong with Your Cold Storage
An Inconsistent Temperature
Something that you always need to do when it comes to cold storage is monitor the temperature. After all, you’re trying to store items at a certain temperature to keep them at their best. If you notice that the temperature keeps fluctuating and dropping, this can mean that there’s a problem. It’s important for the quality of your items to have this seen by a professional immediately.
Larger Energy Bills
Have you noticed that your energy bills have spiked recently? Yes, the prices are rising. But, if this is a huge jump, it could indicate that something is wrong with your cold storage. In other words, it’s having to work harder than normal to maintain the right environment. Do some further investigation to see what the problem could be. It could mean that components need to be replaced.
New Noises
There are always going to be some noises coming from cold storage when they’re running. But, if you notice new noises that aren’t normal, this is a cause for concern. In particular, you don’t want to hear banging or grinding sounds. This can indicate that the motor is having an issue and if you don’t get it fixed, it could break down completely.
Conclusion
Creating a cold room emergency response plan is a critical step in safeguarding your business from unexpected failures. By anticipating potential risks, setting clear protocols, and ensuring your team is well-prepared, you can minimise the impact of cold room issues and keep operations running smoothly. A well-thought-out plan not only protects your goods but also gives you peace of mind, knowing that you can respond quickly and efficiently in any emergency.