How Rubber Injection Molding Machines Help Reduce Production Costs
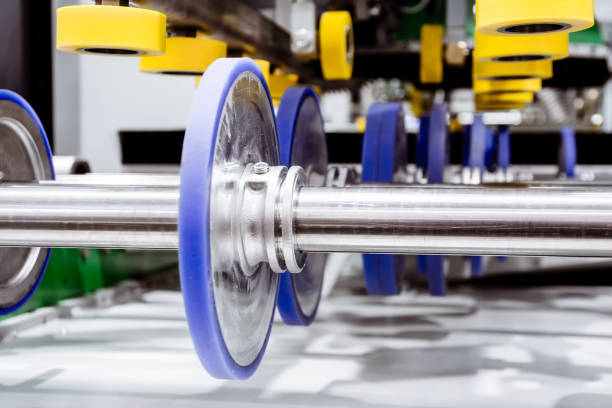
Rubber grinding machines are essential gear in the construction industry. They make the process of making rubber components quicker and more efficient. However, one of the most significant blessings is how those devices reduce manufacturing costs. Let’s take a better look at how that is finished. Working with a reliable injection molding machine manufacturer can help companies save money in several ways. Here’s how these machines help reduce production costs
Less Waste
A high-quality rubber injection molding machine is exact. The proper amount of rubber is used for every product, which means extra or no waste. Reducing waste allows agencies to save money on infrastructure.
Faster Production
These machines work quickly. Many rubber elements may be produced in a short period. Faster production means businesses can produce extra merchandise without spending more on hard work or machinery, reducing universal production fees.
Lower Labor Costs
Rubber rolling machines are generally automatic. This means that fewer people are needed to run their enterprise. With fewer guide paintings required, companies can shop at hard work costs. In addition, while most of the paintings are accomplished with machines, there are fewer mistakes.
Energy Efficiency
Many contemporary rubber rolling machines are energy-green. This means that much less energy is used to run them, which reduces energy fees. Over time, those electricity financial savings add up, helping to lower usual production charges.
Longer Machine Life
These gadgets are designed to remain. They require less protection and renovation in comparison to older machines. A longer-lasting system approach that groups don’t need to spend an awful lot on substitute or repair parts, extensively decreasing production expenses.
Durable and Long-Lasting
Rubber rolling machines are designed to last. Less frequent protection is required, saving organizations money on preservation. The longer the system runs smoothly, the less it costs to replace it.
Types of Rubber Injection Molding Machines
Hydraulic Injection Machinery:
- These machines use water pressure to inject rubber into the molds. They are regularly used because they are powerful and can handle hundreds of pounds.
Electric Injection Machinery:
- These machines use electric cars rather than hydraulics. They are speedy, quiet, and power-green, making them great for excessive-velocity manufacturing.
Mixed rolling generators:
- The hybrid tool combines components of hydropower. They provide both benefits, making them a versatile alternative for exceptional producers’ wishes.
Uses of Rubber Injection Molding Machines
Automotive Services:
- Rubber injection molding machines produce automotive elements, including seals, gaskets, and tires. These machines ensure fast and correct part manufacturing.
Medical Services:
- In the scientific field, those devices are used to manufacture rubber parts, such as scientific seals and sealants. Their high accuracy makes them outstanding substances for scientific devices.
Applications:
- Injection molding machines are used to make regular objects, such as rubber grips, kitchen tools, and rubber toys. These devices offer manufacturers great versatility.
Electronics Services:
- These gadgets fabricate rubber parts, buttons, and defensive seals in digital gadgets. They contribute to the sturdiness and durability of electronics.
Advantages
-
High accuracy:
This machine provides superb accuracy, ensuring that the rubber parts are sized accurately. This reduces waste and improves product quality.
-
Quick tactics:
Many rubber elements are synthetic quickly, supporting companies in meeting high demand immediately.
-
Energy Efficiency:
Hybrid electricity uses much less energy, supporting lessening electricity payments and ensuring environmentally friendly operations.
-
Low guide hard work:
Because many machines are automated, fewer operators are required to perform them, lowering labor fees and human blunders.
-
Multi-motive functions:
Different devices, including hydraulic, electrical, and hybrid equipment, allow agencies to choose only that exception for exceptional manufacturing strategies.
2. Disadvantages
-
High begin-up costs:
The price of these gadgets can be huge, particularly for advanced devices. This may be an undertaking for small companies.
-
Maintenance Requirements:
While complex, those devices require everyday upkeep that could boom typical charges.
-
Complex planning:
Installation and programming of the devices can be complex, and operators might also require specialized training to perform them nicely.
Conclusion
Rubber rolling equipment plays a crucial role in decreasing manufacturing costs. They are accurate, rapid, require minimum exertions, and are strength efficient. Using those devices lets groups produce more fantastic products at lower prices, making them innovative funding for any enterprise.