Understanding and Mitigating Risks in Workplace Material Handling
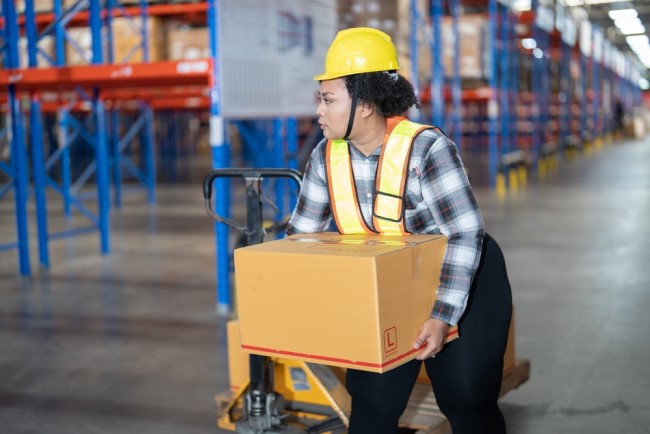
In many workplaces, the handling and movement of loads are essential tasks. Whether in warehouses, construction sites, or manufacturing facilities, material handling introduces a variety of physical risks for employees. These risks, if not managed effectively, can lead to serious injuries and long-term health issues. Common injuries result from physical strain, improper handling techniques, and inadequate equipment, often impacting the back, shoulders, and other vulnerable areas of the body. To prevent injuries and improve workplace safety, it is crucial to understand these risks and implement effective mitigation strategies.
Musculoskeletal Disorders (MSDs): Causes and Prevention
One of the primary risks associated with material handling is musculoskeletal disorders (MSDs), which frequently affect the back, shoulders, arms, and wrists. These injuries are often due to repetitive lifting, maintaining awkward postures, or applying excessive force over prolonged periods. Poor ergonomics or lack of training exacerbates these problems, leading to strains, sprains, and sometimes even chronic pain.
To minimize MSDs, employees should be provided with ergonomic training that emphasizes safe lifting techniques. This includes teaching workers to lift with their legs, not their backs, and to maintain a neutral posture to reduce strain on the spine. Establishing maximum weight limits for manual lifting and encouraging team lifting for heavier items can also reduce physical strain. Additionally, workplaces can invest in assistive equipment like dollies, hand trucks, pallet jacks, or forklifts. By integrating these tools and practices, organizations can significantly reduce the risk of MSDs among employees.
Preventing Slips, Trips, and Falls in Material Handling
Handling heavy or bulky items often obstructs a worker’s view, making it difficult to detect hazards on the floor. This increases the risk of slips, trips, and falls, especially in crowded or poorly maintained work areas. Injuries from falls can be severe, particularly when heavy objects are involved.
Clear walkways and proper lighting are essential to creating a safer environment. Keeping floors free of clutter, spills, and any obstructions reduces the likelihood of accidental falls. Equipping employees with slip-resistant footwear also enhances stability, especially in slippery or uneven conditions. It is equally important to secure loads properly so that they do not shift unexpectedly, potentially destabilizing workers. By prioritizing these preventive measures, employers can make material handling tasks less hazardous and protect workers from potentially life-threatening falls.
Avoiding Crush and Pinch Injuries with Safe Handling Practices
Crush and pinch injuries are another serious risk in material handling environments, particularly when moving large or heavy items or operating machinery. Employees can get caught between a load and another surface, resulting in injuries to hands, feet, or even more critical areas.
Establishing designated zones for material movement and storage can significantly reduce crush and pinch injuries by controlling the flow of activity and restricting unauthorized access. Communication is also key; workers should use hand signals or radios to maintain awareness of each other’s locations, especially when visibility is limited. Providing protective equipment such as gloves can help minimize the impact of incidental contact. By implementing these safety zones and clear communication protocols, organizations can reduce the occurrence of these potentially severe injuries.
Managing Overexertion: Preventing Strains and Sprains
Overexertion injuries, especially to the lower back and shoulders, are common when employees attempt to lift, push, or pull loads that exceed their physical capabilities. This often occurs in fast-paced environments where workers may feel pressured to handle multiple heavy items over an extended shift.
To mitigate this risk, training employees to assess loads and recognize their physical limits is essential. Encouraging the use of mechanical aids, such as dollies or forklifts, can relieve the physical burden on workers. Additionally, allowing for regular breaks and pacing tasks can prevent fatigue, a major contributor to overexertion injuries. By fostering a workplace culture that values safe practices over speed, organizations can protect workers from strains and sprains.
Handling Hazardous Materials Safely
When material handling involves hazardous substances—like chemicals, sharp objects, or potentially toxic materials—the risk of injury extends beyond physical strain. Workers may face additional dangers from spills, inhalation, or accidental contact with hazardous materials.
Providing personal protective equipment (PPE), such as gloves, goggles, and masks, is essential for protecting employees from these risks. Hazardous materials should be stored in secure, leak-proof containers specifically designed for safe handling. Furthermore, employees must be trained in proper handling techniques and emergency procedures for dealing with hazardous materials. This combination of protective gear, secure storage, and training helps prevent incidents involving dangerous substances.
Addressing Repetitive Motion Injuries
Repetitive motion injuries (RMIs) are common in tasks that require employees to perform the same actions repeatedly, leading to strain in the wrists, elbows, and shoulders. Without breaks or variation, these tasks can result in chronic pain and decreased productivity.
To prevent RMIs, rotating tasks among employees is a simple yet effective solution that allows workers to rest specific muscle groups and avoid overuse. Adjustable workstations that accommodate various body positions can also reduce repetitive motion. Implementing a stretching program at the beginning of each shift can further alleviate tension and improve flexibility, helping employees stay healthier and more resilient.
Ensuring Proper Use of Equipment
Using equipment like forklifts, pallet jacks, or hoists incorrectly can lead to injuries for both operators and those nearby. Inexperienced or improperly trained employees are at a higher risk of accidents while operating heavy machinery.
Organizations should ensure that employees receive thorough training and certification before using equipment. Regular inspections and maintenance help identify potential malfunctions before they cause accidents. Clear signage and warning labels can remind operators of safe usage guidelines. By promoting proper equipment use, companies can prevent injuries and maintain a safer work environment.
Conclusion
Workplace material handling presents a variety of risks, but with a proactive approach, these hazards can be managed effectively. By providing training, implementing ergonomic solutions, and encouraging a culture of safety, organizations can significantly reduce the likelihood of injuries. Ensuring that employees are equipped with the right tools, training, and support is key to maintaining a safe, productive workplace where risks are minimized and employees’ well-being is prioritized.