The Role of Precision Injection Molding in Aerospace Parts Manufacturing
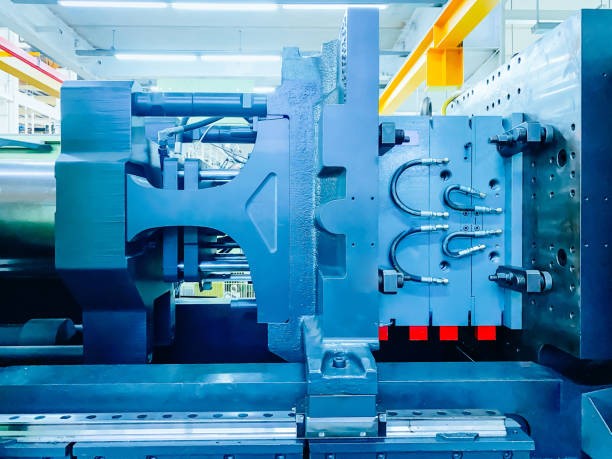
The aerospace industry is very stringent in its requirement for parts. This is why there is a need for accuracy when manufacturing parts and components and this is where precision injection molding comes in. This method allows manufacturers to stick to the required standard while still producing a large number of parts for the industry while still keeping the costs low. With this method, you can produce pretty much any component that the aircraft needs from the exterior to the inside of the plane. It has its advantages and today, we take you on a journey to discover the role of injection molding in aerospace parts manufacturing.
What is Precision Injection Molding?
Precision injection molding is a type of injection molding that produces parts and components with high standards requirements, surface quality, and dimensional accuracy. It produces an accuracy that can reach 0.01mm or less. So to make a precision product it is important to strictly control major factors such as the raw materials used for precision injection, the mold design, and the molding process coupled with the technician’s level of expertise.
Precision injection molding typically requires the dimensional accuracy of the products to be between 0.01 to 0.001mm. They also require high injection speed and pressure to ensure that the product produced meets the high-quality standards required.
On the other hand, general injection molding does not need high dimensional accuracy and relies on the standard of being able to be assembled. The final product may require secondary processing such as oil spraying to improve the appearance when necessary.
General molding machines also do not require special precision injection molding or specified materials and thermoplastics can be used to produce the part.
The key features of procession molding include parts made with tight tolerances ensuring that the manufactured component has minimal variation which is crucial for it to fit precisely. It also utilizes advanced materials such as polymers which will have low shrinkage during cooling ensuring that the dimensions are precise. Precision injection molding also ensures that you can make intricate shapes which are often impossible to achieve when using the general injection molding.
Through these features, the aerospace industry ensures that there is a stringent manufacturing process while using high-quality molds and machinery. This method of manufacturing guarantees that the aerospace industry exceeds standards and that the parts are reliable thus contributing to safer and more efficient aircraft.
Benefits of Precision Injection Molding in Aerospace
The benefits of precision injection molding by factory such as Kemal are similar to the benefits of injection molding used in other industries. They are:
1. Low-cost production of large quantities. The primary benefit of using precision injection molding is that you can produce a large number of parts and components at a lower cost as the cost per piece is cheaper.
2. There is tight tolerance. You can expect extremely high tolerance as low as +/-0.001mm meaning you can produce large quantities with minimal variations in dimensions or quality.
3. Precision injection molding can utilize a wide variety of materials which is why it can be applied for many aerospace parts manufacturing. These materials include Nylon, PC/ABS blends, Polycarbonate, polyethylene, PBT, Polypropylene, Polyvinyl Chloride(PVC), Glass Filled Nylon, ABS, HDPE, Acetal(Delrin), and Soft Durometer Materials.
4. Another benefit of using precision molding is that you are capable of creating intricate and customized designs that other manufacturing methods may not achieve. This is due to the fact that the molten raw material is injected into the mold at high pressure and speed.
Key Aerospace Applications of Precision Injection Molding
In the aerospace industry precision injection molding is necessary due to the need to produce parts that are strong and impact-resistant. Applications of precision injection molding ensure that components meet stringent performance and safety standards.
Parts such as brackets frames and housing are important for the aerospace industry. With precision injection molding you can manufacture components to be strong while still being lightweight thus enhancing the overall performance of the airplane and still maintaining the structural integrity.
Another application is in the engine components such as nozzles, turbines, and seals which must withstand extreme pressure and temperature. With precision injection molding, you can make these parts using heat-resistant materials ensuring that the part or component is durable thus ensuring optimal performance.
In the fuel and hydraulic systems also need parts that fit precisely to ensure that there is no leaking. Through precision injection molding you can create these components ensuring that the engines can function under varying temperatures and pressure.
Precision injection molding can also be used to make seating, panels, and consoles which need to be durable and aesthetically appealing. Using this method you can strike this delicate balance without compromising the functions of the aircraft.
Conclusion
Precision injection molding contributes significantly to the aerospace industry as it has the advantage of being super precise. Through it, you can create high-quality parts and components. This ensures that you can meet the stringent requirements that are needed for making aerospace components. When making these components, you can optimize weight and performance while maintaining the industry standards making it the best option for the aerospace industry.
As technology keeps on advancing, then you can expect that precision injection molding will grow and be adapted to other fields, promoting innovation and development in the manufacturing industry.