Optimizing Yield in Semiconductor Manufacturing: Best Practices and Techniques
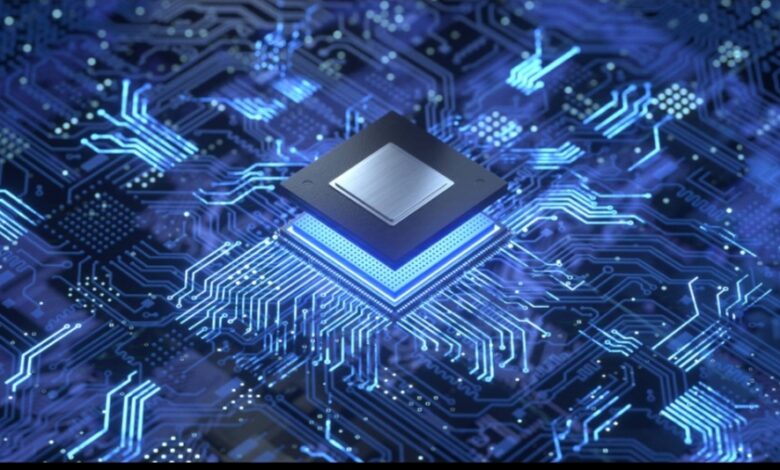
Yield in semiconductor manufacturing signifies the proportion of functional chips successfully produced from a wafer batch. High yield is critical for profitability, efficiency, and competitiveness within the semiconductor industry, as even small yield improvements translate into substantial cost savings and market advantages. Mastering the semiconductor production process is fundamental to achieving these gains.
Several factors influence yield within the semiconductor production process. These include process variability, which can lead to defects; the performance and precision of manufacturing equipment; the quality of materials used; and the complexity of the designs themselves.
Best Practices for Enhancing Yield
Optimizing yield in the semiconductor manufacturing process demands a holistic strategy. Advanced process control (APC) systems and real-time monitoring are crucial for detecting and minimizing variations, ensuring the stability and consistency of the entire semiconductor production process. Early defect detection, facilitated by methods such as automated optical inspection (AOI) and efficient defect classification, is paramount. Timely corrective actions minimize waste and enhance efficiency throughout the semiconductor manufacturing process. Design for Manufacturability (DFM) plays a vital role. By incorporating manufacturing constraints into the design phase, engineers streamline the semiconductor production process, improve yield, and reduce costs.
Advanced Techniques for Yield Optimization
As semiconductor production processes become increasingly complex, advanced techniques are essential. Statistical Process Control (SPC) tools analyze manufacturing data, identify trends, and enable proactive corrective actions to maintain high yield levels within the semiconductor production process. Machine learning and AI, through analysis of large datasets, predict yield outcomes and suggest process adjustments for data-driven optimization of the semiconductor manufacuring process. Cross-functional collaboration between design, engineering, and Manufacture teams is vital for identifying and implementing process improvements, optimizing the semiconductor production process, and improving overall yield.
Challenges and Solutions in Yield Optimization
Yield optimization in semiconductor manufacturing faces continuous challenges. The increasing complexity and miniaturization of semiconductor devices make maintaining high yields increasingly difficult. Innovative solutions are needed to enhance process control, improve defect detection, and adapt to the ever-changing demands of the semiconductor production process. Supply chain considerations, encompassing material quality and logistics, significantly impact the reliability of the semiconductor production process. Stringent quality checks and improved logistics planning mitigate these supply chain risks. A culture of continuous improvement and innovation is essential for adapting to emerging challenges and refining manufacturing processes to sustain high yield levels in the dynamic semiconductor manufacturing process.