Monel Metal Welding Guide: Tips for a Strong, Durable Bond
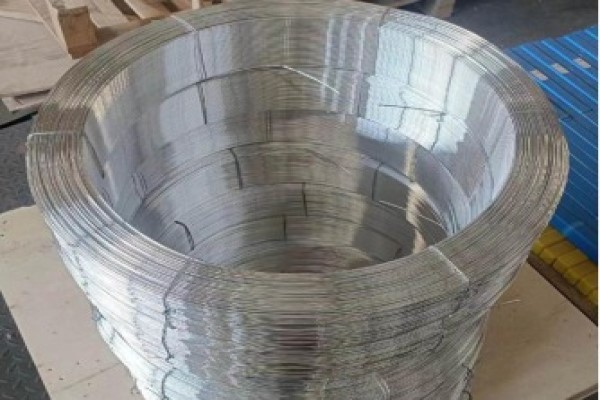
Monel metal is renowned for its exceptional corrosion resistance, strength, and durability, making it a popular choice for industries such as marine engineering, chemical processing, and aerospace. However, welding Monel metal presents a unique set of challenges that must be carefully managed to ensure a strong and durable bond. In this comprehensive guide, monel suppliers explore the best practices for welding Monel metal, providing essential tips to help you achieve optimal results in your welding projects.
What Is Monel Metal?
Monel metal is a group of nickel-based alloys that consist primarily of nickel (up to 67%) and copper, with small amounts of iron, manganese, carbon, and other elements. The two most common types of Monel metal are Monel 400 and Monel K-500.
Monel 400: This alloy is highly resistant to a wide range of corrosive environments, including seawater and acidic solutions. It is commonly used in marine and chemical industries.
Monel K-500: This alloy contains additional elements such as aluminum and titanium, which enhance its strength and hardness while retaining the corrosion resistance of Monel 400. It is often used in oil and gas applications, aerospace, and pump shafts.
Given the unique properties of Monel metal, it is a preferred material in industries that require superior corrosion resistance and mechanical strength. However, its high nickel content makes welding Monel metal more challenging than welding other metals like stainless steel or aluminum.
The Challenges of Welding Monel Metal
Welding Monel metal requires a specific approach due to its susceptibility to cracking, its high thermal conductivity, and the potential for porosity in the weld joint. Here are some common challenges you might face when welding Monel metal:
Cracking: Monel metal is prone to hot cracking, particularly in the heat-affected zone (HAZ). Proper control of heat input is essential to minimize this risk.
Porosity: When welding Monel metal, gases such as nitrogen, hydrogen, or oxygen can become trapped in the weld pool, leading to porosity. This can weaken the weld joint and compromise its integrity.
Thermal Conductivity: Monel metal has high thermal conductivity, which means heat dissipates quickly from the weld zone. This requires careful attention to heat input and cooling rates to avoid defects.
Understanding these challenges is the first step in successfully welding Monel metal. Now, let’s look at the specific techniques and tips that can help ensure a strong, durable bond.
Best Practices for Welding Monel Metal
Choose the Right Welding Process
Several welding processes are suitable for Monel metal, but some methods are better suited to specific applications than others. The most commonly used welding methods for Monel include:
Gas Tungsten Arc Welding (GTAW/TIG): This method is highly recommended for welding Monel metal due to its precise control over heat input and its ability to produce clean, high-quality welds. GTAW is especially useful for thinner Monel metal components.
Gas Metal Arc Welding (GMAW/MIG): For thicker Monel metal components, GMAW is often used. This process allows for faster welding speeds and is well-suited for high-production environments.
Shielded Metal Arc Welding (SMAW): SMAW, or stick welding, is another option for welding Monel metal, particularly in field applications. However, care must be taken to select the correct filler material and maintain proper heat control.
Each of these methods has its strengths, but TIG welding tends to provide the best results for Monel metal due to its precise control over heat and the ability to work with thinner materials.
Select the Appropriate Filler Material
Choosing the correct filler material is crucial when welding Monel metal. For Monel 400, it’s recommended to use Monel 60 filler metal, which has a similar composition and ensures a compatible weld. For Monel K-500, a filler metal with higher strength, such as INCO 82, may be used.
Monel 60: A nickel-copper alloy filler material, Monel 60 is commonly used for welding Monel 400. It provides good corrosion resistance and strength, ensuring that the weld joint matches the properties of the base material.
INCO 82: This nickel-based filler material is often used when welding Monel K-500. It provides a strong, durable bond and is resistant to corrosion and cracking.
By selecting the right filler material, you can ensure that the weld joint retains the desirable properties of Monel metal, including corrosion resistance and strength.
Control Heat Input
Controlling heat input is essential when welding Monel metal to prevent hot cracking and other weld defects. Excessive heat input can lead to grain growth in the heat-affected zone, which increases the likelihood of cracking.
Maintain Low Heat Input: Use lower amperage settings to reduce heat input and prevent overheating the material. This is particularly important when welding thin sections of Monel metal.
Interpass Temperature Control: Maintain an interpass temperature below 300°F (150°C) to prevent excessive heat buildup. This helps to control the cooling rate and minimizes the risk of cracking in the heat-affected zone.
By carefully controlling heat input, you can reduce the risk of hot cracking and ensure a strong, durable weld joint.
Use Proper Shielding Gas
Selecting the right shielding gas is critical for achieving a quality weld when working with Monel metal. Shielding gas prevents contamination of the weld pool by atmospheric gases such as oxygen, nitrogen, and hydrogen, which can lead to porosity and other defects.
Argon: Pure argon is often used as the shielding gas for TIG welding Monel metal. It provides excellent protection for the weld pool and helps prevent porosity.
Argon-Helium Mixture: In some cases, a mixture of argon and helium can be used to improve heat transfer and penetration. This is particularly useful when welding thicker sections of Monel metal.
Using the correct shielding gas helps ensure a clean, defect-free weld with good penetration and strength.
Clean the Material Thoroughly
Before starting the welding process, it’s important to thoroughly clean the **Monel metal** surfaces. Any contamination, such as oil, grease, or dirt, can negatively impact the weld quality and increase the risk of porosity.
Remove Surface Contaminants: Use a wire brush or solvent to clean the surface of the material before welding. Make sure to remove any oxides, oils, or other contaminants that could affect the weld.
Use Clean Tools: Ensure that all tools used for cleaning and preparing the material are clean and free from contamination to prevent introducing foreign particles into the weld pool.
Proper surface preparation is key to ensuring a strong and defect-free weld when working with Monel metal.
Consider Preheating for Thick Sections
For thicker sections of Monel metal, preheating the material can help reduce the risk of cracking and improve weld quality. Preheating helps to equalize the temperature of the material, reducing thermal stress during the welding process.
Preheat Temperature: A preheat temperature of 200°F to 400°F (93°C to 204°C) is often recommended for thick Monel metal sections. This helps to reduce the thermal gradient and minimize the risk of cracking.
Preheating can be particularly beneficial for thicker components and joints that are prone to cracking.
Common Mistakes to Avoid When Welding Monel Metal
Welding Monel metal can be challenging, and there are several common mistakes that can compromise the quality of the weld. Here are a few things to avoid:
Using Incorrect Filler Material: Always select the appropriate filler material for the grade of Monel metal you are welding. Using an incompatible filler can result in weak joints and increased risk of cracking.
Excessive Heat Input: Applying too much heat can cause the material to overheat, leading to grain growth and increased susceptibility to cracking.
Inadequate Shielding Gas: Failing to provide adequate shielding gas can result in porosity and other weld defects. Always ensure that the gas flow is sufficient to protect the weld pool from atmospheric contamination.
By avoiding these common mistakes, you can improve the quality and durability of your Monel metal welds.
Conclusion
Welding Monel metal requires a thorough understanding of its unique properties and the challenges it presents. By choosing the right welding process, controlling heat input, using the appropriate filler material, and ensuring proper shielding gas and material preparation, you can achieve strong, durable welds that maintain the exceptional corrosion resistance and strength of Monel metal.