Leveraging Flexible Manufacturing Systems in Industrial Automation
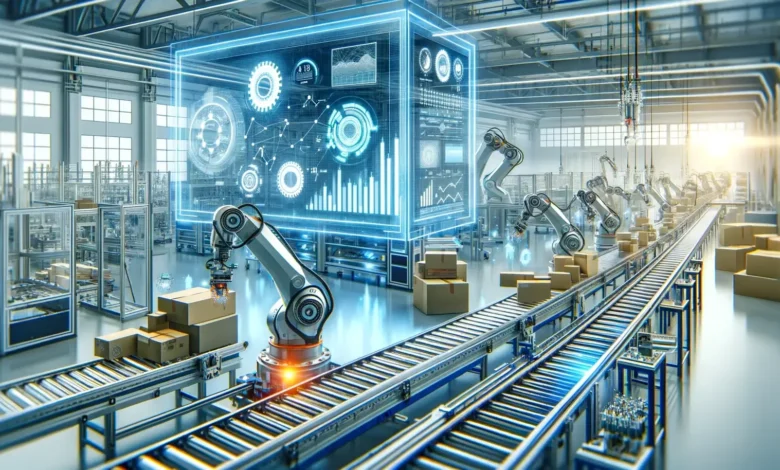
In an era dominated by rapid technological advancements and shifting market demands, flexibility within manufacturing processes is more crucial than ever. Flexible Manufacturing Systems (FMS) have become a cornerstone in modern industrial automation, enabling manufacturers to respond swiftly and efficiently to varying production needs without sacrificing quality or throughput. At the heart of these systems are technologies like servo controllers, which enhance precision and adaptability, essential for dynamic manufacturing environments. This article delves into the principles, benefits, and challenges of implementing FMS in industrial automation, highlighting the critical role of servo controllers.
Understanding Flexible Manufacturing Systems
Flexible Manufacturing Systems represent an integrated approach to manufacturing that is designed to react and adapt to changes with minimal intervention and cost. An FMS typically consists of several robotic stations and CNC machines that are interconnected through an automated material handling and storage system, all controlled by a central computer system. The flexibility in FMS arises from its ability to produce a variety of parts without the need for major retooling, making it ideal for industries that require a mix of products in variable volumes.
Core Components of Flexible Manufacturing Systems
CNC Machines
Computer Numerical Control (CNC) machines form the backbone of any FMS, providing the high precision machining capabilities essential for modern manufacturing. These machines perform various tasks such as drilling, milling, and lathing, driven by detailed instructions from computer software.
Robotic Arms
Robotic arms in an FMS are versatile tools used for tasks ranging from welding and assembly to material handling and product inspection. They are programmed to perform multiple tasks with high repeatability and precision.
Automated Material Handling Systems
Conveyors, Automated Guided Vehicles (AGVs), and shuttle systems ensure the smooth flow of materials between different stations in the FMS. These systems are crucial for reducing idle times and enhancing the efficiency of the production process.
Servo Controllers
Servo controllers are critical in FMS for controlling the speed, position, and torque of servo motors that drive the CNC machines and robotic arms. They allow precise movements and adjustments, which are essential for the high-quality standards required in flexible manufacturing. By adjusting parameters in real-time, servo controllers ensure that equipment operates optimally across different production scenarios.
Computer Systems and Software
The integration and coordination of all components within an FMS are managed by sophisticated computer systems and software. This software handles everything from production scheduling and real-time monitoring to quality control and maintenance management.
Benefits of Flexible Manufacturing Systems
Enhanced Productivity
FMS allows for continuous production with minimal downtime. The ability to quickly switch between product types or adjust production volumes without extensive downtime for setup changes significantly boosts productivity.
High-Quality Production
The precision of CNC machines and robotic arms, coupled with the control provided by servo controllers, ensures products are manufactured with high accuracy and consistency, meeting strict quality standards.
Reduced Costs
Although the initial setup cost for an FMS can be high, the system contributes to long-term savings by reducing labor costs, minimizing waste, and lowering the costs associated with inventory and storage.
Greater Market Responsiveness
With the ability to alter production schedules and product types quickly, manufacturers can respond more effectively to market changes and customer demands, enhancing competitiveness and customer satisfaction.
Challenges in Implementing Flexible Manufacturing Systems
High Initial Investment
The cost of setting up an FMS, including the purchase of CNC machines, robotic arms, and sophisticated control systems like servo controllers, can be substantial. This makes it a significant investment that companies need to plan for meticulously.
Technical Complexity
Implementing and maintaining an FMS requires a high level of technical expertise. Staff need to be trained not only on the operation of complex machinery but also on system troubleshooting and maintenance.
Integration Issues
Integrating new FMS components with existing production systems can be challenging, especially if the existing infrastructure is outdated. This may require additional modifications or upgrades, increasing the complexity and cost of implementation.
Conclusion
Flexible Manufacturing Systems represent a transformative approach in industrial automation, offering unmatched flexibility and efficiency. The incorporation of advanced technologies like servo controllers like the DKC22.3-200-7-FW within these systems allows businesses to maintain high precision in production processes, adapt quickly to changing market conditions, and optimize operational efficiency. As manufacturing demands continue to evolve, the role of FMS in industrial automation will become increasingly prominent, driving innovation and sustainability in manufacturing practices worldwide. Embracing these systems is not just about enhancing production capability—it’s about positioning a company to thrive in the future landscape of manufacturing.