If Evaporator Is Flooded the Superheat Will Increase: Understanding Refrigeration System Dynamics
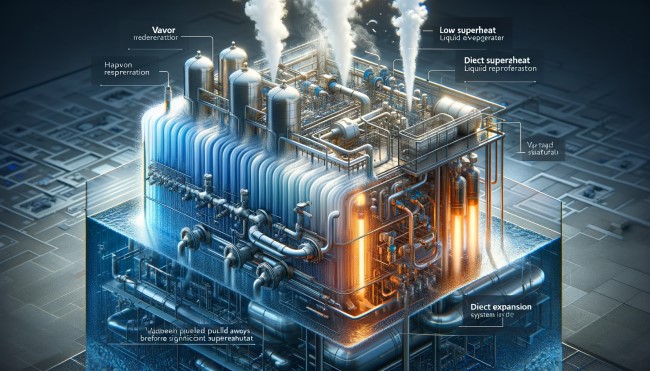
In the world of refrigeration systems, understanding the relationship between superheat and evaporator performance is crucial. This article dives deep into how a flooded evaporator impacts superheat, breaking down technical details and offering insights into system efficiency and safety.
Introduction to Refrigeration Systems and Superheat
Superheat refers to the difference between the actual temperature of refrigerant vapor and its saturation (boiling) temperature. It plays a critical role in ensuring that refrigerant entering the compressor is in a vapor state, thereby preventing damage to the compressor.
What Happens in a Flooded Evaporator?
A flooded evaporator means more refrigerant is entering the system than can be evaporated, causing liquid refrigerant to remain in the evaporator. In an ideal system, the refrigerant absorbs heat, evaporating completely and leaving the evaporator as a vapor. However, in a flooded scenario, the refrigerant doesn’t completely vaporize, leading to excess liquid refrigerant that can drastically alter the superheat levels.
Superheat in a Flooded Evaporator
In a flooded evaporator, the superheat decreases, rather than increases. Superheat is typically minimal or non-existent because the refrigerant does not fully vaporize before exiting the evaporator. As a result, less heat is required to raise the temperature of the refrigerant above its boiling point.
Despite the common misconception that flooding leads to increased superheat, the opposite is true. The system efficiency is optimized by keeping the refrigerant in a mostly liquid state, utilizing the full evaporator surface for heat transfer.
The Role of Metering Devices in Flooded and DX Systems
In direct expansion (DX) systems, metering devices ensure that only the necessary amount of refrigerant is allowed into the evaporator. This creates a balance between heat absorption and vaporization. However, in flooded systems, the metering devices function differently. Instead of restricting the flow of refrigerant, they allow excess liquid refrigerant into the evaporator.
The objective in a flooded system is to keep as much of the evaporator coil filled with liquid refrigerant as possible. This increases the heat transfer efficiency but requires careful management to prevent liquid refrigerant from reaching the compressor.
Why Flooding Reduces Superheat
Flooded evaporators are designed to pull the vapor out before significant superheating can occur. This technique optimizes the heat absorption process, as liquid refrigerant absorbs more heat than vapor. A flooded evaporator allows the system to operate with a higher refrigerant flow rate, sometimes up to 200% more than the heat load requires. This is significantly more refrigerant than would be used in a traditional DX system, where maintaining superheat is crucial to prevent liquid from damaging the compressor.
The Importance of Compressor Safety
Flooded evaporators are also designed with compressor protection in mind. Since superheat is kept to a minimum, there’s less risk of overheating the refrigerant, which in turn reduces the discharge temperature of the compressor. This design is particularly beneficial in systems using ammonia, where high discharge temperatures can cause operational challenges. By controlling superheat, the evaporator ensures the compressor remains adequately cooled, prolonging its life and efficiency.
Benefits of Flooded Evaporators
- Enhanced Heat Transfer Efficiency: Flooded evaporators maximize the surface area available for heat absorption. By keeping the refrigerant in a saturated state, they allow for more efficient heat transfer compared to systems that rely on superheated vapor.
- Lower Compressor Workload: Since the refrigerant enters the compressor with minimal superheat, the compressor doesn’t need to work as hard to manage high temperatures, leading to increased longevity and reduced energy consumption.
- Lower Discharge Temperatures: Especially in systems using ammonia as a refrigerant, maintaining minimal superheat keeps discharge temperatures low, which is crucial for avoiding overheating and extending the system’s operational life.
Challenges of Flooded Evaporators
- Oil Management: One of the biggest challenges in flooded evaporator systems is managing oil. Since oil doesn’t evaporate like refrigerant, it can accumulate in the evaporator, reducing efficiency. To mitigate this, oil separators are used to minimize the amount of oil that enters the evaporator, and systems are designed to siphon off any trapped oil and return it to the compressor.
- Complex System Design: Flooded evaporators require more complex controls, such as liquid level sensors and float valves, to manage the flow of refrigerant effectively. These systems are more intricate than standard DX systems, requiring skilled technicians to design, maintain, and troubleshoot.
- Risk of Floodback: If too much liquid refrigerant is allowed into the compressor, it can cause mechanical damage, a condition known as floodback. Proper design and maintenance of the system are critical to avoiding this issue.
How to Prevent Issues in Flooded Evaporators
- Regular Maintenance: Keep heat transfer surfaces clean and maintain proper airflow across both the evaporator and condenser. Dirty coils can affect the system’s ability to maintain proper superheat, leading to performance issues.
- Proper Insulation: Ensure the suction line is well insulated to prevent unnecessary heat gain and minimize superheat. Thick insulation helps keep the system operating efficiently by reducing the load on the compressor.
- System Monitoring: Use sensors to monitor liquid levels and ensure that the evaporator is performing optimally. These sensors can automatically adjust refrigerant flow to prevent flooding and optimize efficiency.
Conclusion: Maximizing Efficiency in Flooded Evaporators
In conclusion, flooded evaporators are a highly efficient means of managing heat transfer in refrigeration systems, particularly in industrial applications. By minimizing superheat, they enhance the overall efficiency of the system and protect critical components like the compressor from damage. However, they require careful design and regular maintenance to ensure they operate effectively.
While the misconception that superheat increases in a flooded evaporator persists, the reality is quite the opposite. By maintaining a balance of refrigerant flow and heat absorption, flooded systems can provide robust, long-lasting performance, as long as their unique challenges are properly managed.
Flooded evaporators stand out for their ability to enhance system efficiency and reduce compressor workload, but they are not without their complexities. By understanding their design and operating principles, you can ensure that your system runs smoothly, saving energy and extending the life of your refrigeration equipment.