How Ultrasonic Testing Helps Detect Critical Material Defects
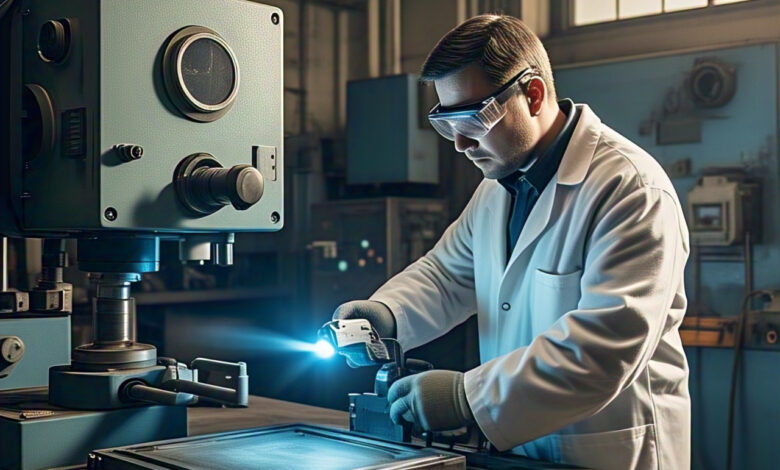
In industries like aerospace, automotive, construction, and energy, the integrity of materials is paramount to ensuring the safety and reliability of structures. Any defects in materials can lead to catastrophic failures, resulting in safety hazards, production downtime, and costly repairs. Ultrasonic testing (UT) is a vital non-destructive testing (NDT) method that detects internal flaws without damaging the material. This article explores how ultrasonic testing identifies critical material defects such as cracks, corrosion, and voids, ensuring the safety and longevity of industrial components.
What is Ultrasonic Testing?
Ultrasonic testing (UT) is a non-destructive testing technique that uses high-frequency sound waves to examine materials for internal defects. The basic principle involves sending sound waves through a material and analyzing the reflections (or echoes) from the waves as they encounter different materials or flaws. The time it takes for the waves to return and their intensity provide valuable information about the internal structure of the material.
UT can detect a wide range of defects that are not visible on the surface, including cracks, corrosion, porosity, delamination, and voids. These defects can significantly compromise the integrity of materials, leading to premature failure. The UT process involves the use of an ultrasonic transducer that generates sound waves at specific frequencies. The data gathered is interpreted to reveal any internal flaws, allowing for accurate defect analysis.
The importance of using UT in industries that rely on critical components cannot be overstated. By identifying defects before they cause significant damage, ultrasonic testing helps prevent catastrophic failures, ensuring the safety of both the public and industrial operations.
How Ultrasonic Testing Detects Critical Defects
Cracks
Cracks are one of the most dangerous material defects. Ultrasonic testing is highly effective in detecting cracks that are often invisible to the naked eye. When ultrasonic waves encounter a crack, they are reflected back differently compared to a solid part of the material. These reflections create distinct patterns that indicate the presence of a crack. The size, depth, and orientation of the crack can be accurately determined, allowing for effective decision-making regarding maintenance or repairs.
Corrosion
Corrosion is a common issue in industries that deal with pipelines, tanks, and pressure vessels. Over time, materials exposed to environmental factors such as moisture, chemicals, or heat can corrode, leading to thinning and weakening of the material. Ultrasonic testing is ideal for measuring the thickness of materials and identifying any areas that have thinned due to corrosion. By identifying corrosion early, UT helps prevent failures in critical infrastructure, such as pipeline ruptures or pressure vessel explosions.
Porosity and Voids
Porosity refers to the presence of internal voids or air pockets within a material. These voids can significantly weaken the structural integrity of materials such as metals and composites. Ultrasonic testing can detect porosity by analyzing the way sound waves travel through the material. If there are voids present, the sound waves will be disrupted or reflected differently. Detecting porosity early on can help prevent catastrophic failures in materials that are critical to industries such as aerospace and automotive.
Ultrasonic testing has been successfully used to identify critical defects in materials used in aircraft engines, pressure vessels, and pipelines. Early detection of these defects allows for prompt maintenance, which can extend the lifespan of the materials and prevent major safety issues.
The Importance of Detecting Defects Early
The early detection of material defects is crucial to maintaining safety and reliability in industrial operations. When defects are identified at an early stage, they can be addressed before they become significant problems that lead to safety hazards, production stoppages, or costly repairs. Ultrasonic testing plays a key role in preventive maintenance programs by allowing businesses to identify defects before they reach a critical stage.
In industries like oil and gas, power generation, and automotive manufacturing, undetected cracks or corrosion can result in catastrophic failures, causing loss of life, environmental damage, and substantial financial costs. For example, a small crack in a pipeline, if left undetected, could lead to a leak or rupture, causing severe damage and a lengthy recovery process. UT helps prevent such outcomes by identifying defects early enough to take corrective action.
Real-life examples of incidents where undetected material defects caused significant losses highlight the importance of proactive defect detection. By adopting ultrasonic testing technologies, industries can greatly reduce the risk of these costly and dangerous failures.
Benefits of Using Ultrasonic Testing for Critical Defect Detection
Non-Destructive Nature
One of the biggest advantages of ultrasonic testing is its non-destructive nature. Unlike other testing methods such as X-ray or destructive testing, UT does not damage or alter the material being tested. This means that the component can continue to be used after the test, saving on material costs and reducing downtime. Non-destructive testing is particularly beneficial in industries where materials are expensive or critical to operations.
Precision and Reliability
Ultrasonic testing is known for its precision and reliability. Using high-performance NDT scanners, inspectors can achieve more consistent and detailed evaluations, even in complex materials or geometries. It can detect even the smallest defects with high accuracy, ensuring that no issue goes unnoticed. This level of precision is crucial in industries where small defects can lead to major failures. UT’s ability to provide reliable, quantifiable results reduces the risk of overlooking critical flaws and ensures that maintenance teams can act on accurate data.
Cost-Effective
While some testing methods can be expensive and time-consuming, ultrasonic testing offers a cost-effective solution. It is quicker, requires less downtime, and is generally more affordable than other methods, such as X-ray testing. Additionally, UT helps prevent expensive repairs and replacements by detecting defects early, ultimately saving businesses money in the long run.
Versatility
Ultrasonic testing is incredibly versatile and can be applied across various industries and materials. Whether it is metals, composites, or plastics, UT can be used to detect defects in a wide range of materials. This versatility makes ultrasonic testing an ideal solution for diverse industries, including aerospace, automotive, construction, and energy.
Conclusion
Ultrasonic testing is vital for detecting material defects like cracks, corrosion, and porosity, helping industries prevent failures and ensure safety. Its non-destructive, precise, and cost-effective nature makes it essential for preventive maintenance. By adopting UT technologies or working with service providers, industries can improve material safety, reduce risks, and avoid costly repairs, ensuring the reliability and longevity of components.