How CMMS Software Reduces Maintenance Backlogs And Downtime
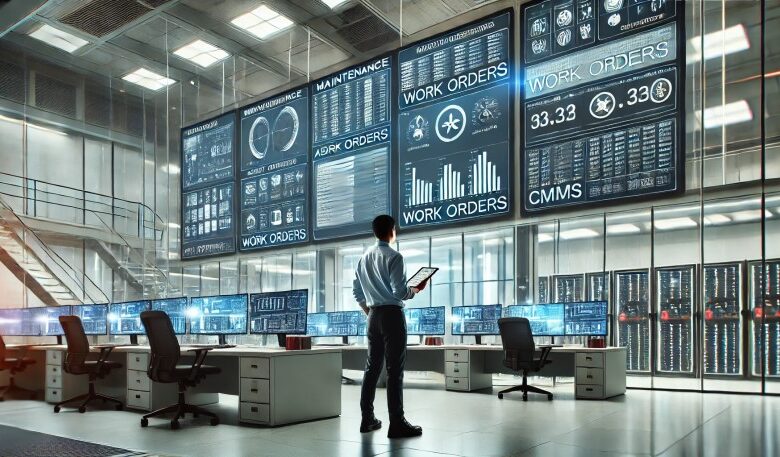
Maintaining maintenance tasks in any facility can be challenging, especially when unexpected breakdowns and backlogs start piling up. Delays in repairs lead to equipment failures, production slowdowns, and increased costs. Without an efficient system to track work orders, schedule preventive maintenance, and manage assets, maintenance teams struggle to stay ahead of issues. These inefficiencies reduce productivity and shorten the lifespan of valuable equipment.
Computerized Maintenance Management System (CMMS) software provides a structured approach to maintenance operations, helping organizations manage workloads more effectively. CMMS Software reduces maintenance backlogs and minimizes downtime by automating work orders, tracking asset health, and scheduling routine tasks. It ensures that teams can focus on high-priority repairs and preventive measures instead of reacting to crises.
Key Ways CMMS Software Prevents Backlogs And Reduces Downtime
CMMS addresses these challenges by improving organization, efficiency, and planning. Here’s how CMMS plays a crucial role in streamlining maintenance processes:
Automated Work Order Management
Traditional work order systems rely on paper records or spreadsheets, making it easy for tasks to get lost, overlooked, or duplicated. CMMS centralizes all work orders in a digital platform, ensuring that requests are logged, tracked, and completed on time. Maintenance teams receive real-time notifications, reducing delays and addressing urgent repairs quickly.
Preventive Maintenance Scheduling
Unplanned breakdowns often stem from a lack of routine maintenance. CMMS allows teams to schedule preventive maintenance based on time, usage, or condition-based triggers. By servicing equipment before problems arise, organizations reduce the risk of costly failures and keep assets running efficiently.
Real-Time Asset Tracking And Performance Monitoring
Aging equipment requires frequent inspections, but tracking each asset manually is impractical. CMMS software provides real-time insights into asset conditions, flagging issues before they cause breakdowns. Maintenance teams can review historical data, identify recurring problems, and make data-driven decisions to extend equipment lifespan.
Inventory And Spare Parts Management
One of the biggest causes of maintenance delays is the unavailability of necessary spare parts. CMMS tracks inventory levels, alerts teams when supplies are low, and automates reordering processes. This ensures technicians have the essential parts when a repair is required, preventing unnecessary downtime.
Labor Resource Optimization
Managing maintenance personnel effectively is crucial for preventing backlogs. CMMS assigns tasks based on technician availability, skill set, and priority level. It helps teams distribute workloads evenly and eliminates bottlenecks caused by scheduling conflicts or inefficient task allocation.
Compliance and Safety Assurance
Regulatory requirements often mandate specific maintenance procedures and missing inspections can lead to fines or safety hazards. CMMS software keeps track of compliance deadlines, generates reports, and ensures maintenance teams follow safety protocols. By maintaining compliance, organizations avoid legal issues and keep equipment operating safely.
Strengthening Long-Term Maintenance Strategies
Beyond handling immediate work orders and reducing downtime, CMMS maintenance software plays a significant role in long-term maintenance planning. It helps organizations transition from reactive to proactive strategies, reducing costs and increasing efficiency.
Maintenance managers gain better control over their operations by leveraging detailed reports and predictive analytics and making informed decisions. Investing in CMMS software is a necessity for sustainable maintenance management.