Exploring the Role of FR4 in PCB Design: Key Properties and the Impact of Dielectric Constant
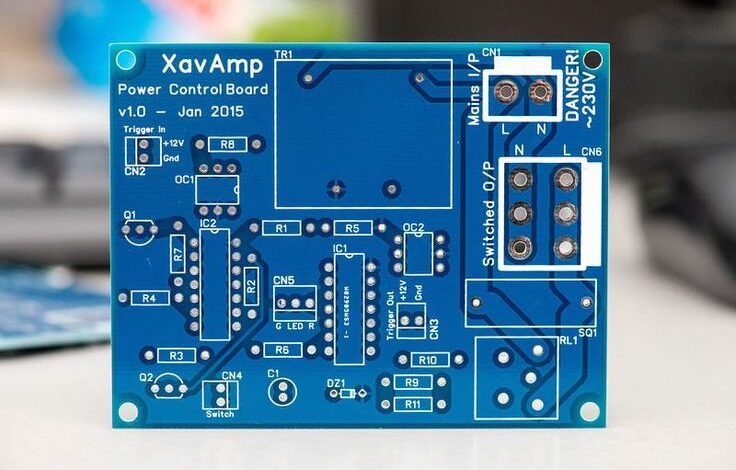
In the world of PCB (Printed Circuit Board) manufacturing, FR4 is one of the most commonly used materials. It has become the standard for most electronic products due to its excellent balance of electrical, mechanical, and thermal properties. Whether you’re designing simple consumer electronics or complex industrial circuits, FR4 offers significant advantages in performance, cost-effectiveness, and durability.
What is FR4 Material?
FR4 is a glass-reinforced epoxy laminate material commonly used in PCB production. It is a composite made of woven fiberglass cloth impregnated with epoxy resin. The “FR” stands for flame retardant, signifying its resistance to combustion, while the “4” refers to the grade of the material as defined by the National Electrical Manufacturers Association (NEMA).
FR4 is popular in PCB manufacturing because it is cost-effective, strong, and insulates well. It also offers excellent resistance to environmental stress factors such as heat, humidity, and mechanical forces.
Properties of FR4 Material PCB
FR4 has several critical properties that make it suitable for PCB applications:
- Electrical Insulation: FR4 is an excellent electrical insulator, which helps to maintain proper isolation between conductive traces on the PCB.
- Mechanical Strength: The glass fibers in FR4 provide mechanical strength, making it durable and less prone to damage from stress or bending.
- Thermal Stability: FR4 can withstand high temperatures, making it ideal for electronics that generate heat during operation.
- Flame Retardant: As a flame-retardant material, FR4 ensures safety by limiting the risk of fire in case of electrical failures.
The Importance of FR4 Dielectric Constant
The dielectric constant (Dk) is one of the key electrical properties of any PCB material. It defines the material’s ability to store electrical energy in an electric field and significantly affects signal integrity, transmission speed, and overall performance of the PCB.
For FR4 material, the dielectric constant is typically in the range of 4.2 to 5.0, although it can vary slightly depending on the specific formulation of the FR4 laminate. Understanding the dielectric constant is crucial in the design of high-speed and high-frequency circuits.
Dielectric Constant (Dk) and Signal Transmission
The dielectric constant directly influences the speed at which signals travel through the PCB’s traces. In simpler terms, the higher the dielectric constant, the slower the signal will travel through the material. This is because a material with a higher Dk will store more electrical energy, which increases the impedance and delays the signal’s propagation.
In high-speed circuits, such as those used in modern consumer electronics, telecommunications, and computing devices, the dielectric constant becomes a critical parameter. Too high or too low of a Dk can result in signal distortion, reflections, and reduced overall performance.
Impact of Dielectric Constant on FR4 PCB Performance
- Signal Integrity: A consistent and stable Dk ensures minimal distortion in high-speed signal transmission. Variations in the dielectric constant across the PCB can lead to signal degradation and loss of information, particularly in high-frequency designs.
- Trace Width and Impedance Control: The dielectric constant affects the width of PCB traces needed to maintain controlled impedance. For high-frequency applications, ensuring that the trace width and the dielectric constant match is crucial for maintaining signal integrity.
- Design Considerations: When designing PCBs that operate at higher frequencies (e.g., RF circuits), the Dk of the material must be carefully considered. FR4’s relatively high Dk can limit its application in high-frequency designs compared to other materials with lower Dk, such as PTFE (Teflon).
Applications of FR4 PCBs
Despite its relatively higher dielectric constant compared to other materials like PTFE, FR4 is widely used for general-purpose PCBs across various industries. It is particularly effective for applications where high-frequency signals are not a primary concern, such as:
- Consumer Electronics: Smartphones, laptops, TVs, and audio equipment.
- Automotive Electronics: Sensors, control units, and infotainment systems.
- Industrial Electronics: Power supplies, motors, and controllers.
- Medical Devices: Monitoring equipment, diagnostic instruments, and wearable devices.
Advantages of Using FR4 Material in PCB Manufacturing
- Cost-Effective: FR4 is significantly cheaper than many other high-performance PCB materials like PTFE or ceramic-based materials.
- Widely Available: FR4 is one of the most widely available PCB materials, ensuring a broad supply chain and fast turnaround times for PCB production.
- Good Electrical and Mechanical Properties: FR4 provides a good balance between electrical performance, mechanical durability, and thermal stability.
- Versatile: Suitable for a wide range of applications from consumer electronics to industrial machinery, as it meets general-purpose requirements.
Limitations of FR4 Material
While FR4 is a versatile and reliable PCB material, it does have certain limitations:
- High Dielectric Constant: For high-frequency applications, the relatively high dielectric constant (4.2–5.0) of FR4 can limit its performance, particularly in RF and high-speed signal applications.
- Limited High-Frequency Performance: At frequencies above 1 GHz, the performance of FR4 can degrade due to signal attenuation and loss.
For more advanced and high-performance applications that require lower dielectric constants and better signal integrity at high frequencies, other materials like PTFE (Teflon) or ceramics might be considered.
Conclusion
FR4 material remains the go-to solution for most standard PCB applications, offering a strong balance of cost, mechanical strength, thermal stability, and electrical insulation. While its dielectric constant of 4.2–5.0 may limit its performance in high-frequency applications, FR4 is an excellent choice for many electronics that do not require extremely high-speed signals. Understanding the dielectric constant and other material properties is essential for optimizing PCB designs and ensuring reliable and high-performance electronic devices.
As PCB technology advances and designs push towards higher frequencies, it is important to understand the material limitations and choose the right material for each specific application. However, for many typical electronic products, FR4 continues to be the best choice in terms of performance, cost, and availability.