Die Casting Technology: Advancements Shaping Modern Manufacturing
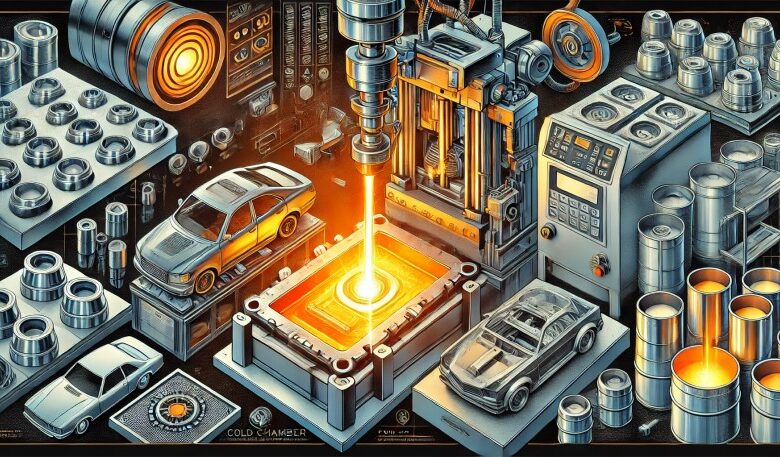
Overview of Die Casting
Die casting is a fascinating process where molten metal is pressed into a mold. It creates strong and precise parts used in many industries, like automotive and aerospace. You’ll learn about what die casting is and the different methods used to bring metal parts to life.
Defining Die Casting
In die casting, molten metal, often aluminum or zinc, is poured into a die or mold. A die is like a detailed cookie cutter, giving the metal its shape. This process is loved for making parts that are both strong and exact.
High pressure is used to fill the mold, making sure every part of it gets filled quickly and evenly. This results in fewer defects and high-quality parts.
It’s a favorite technique in manufacturing because it produces many parts quickly without losing quality. This speed is important in sectors like consumer electronics, where thousands of parts are needed.
Die Casting Methods
There are two main methods in die casting: hot chamber and cold chamber. The hot chamber process keeps the metal near the die, allowing it to be injected quickly. This is great for metals with low melting points, like zinc.
The cold chamber method involves melting the metal in a separate chamber and injecting it into the mold. It’s used for metals like aluminum, which have higher melting points.
Each method is chosen based on the metal used and the product requirements, balancing speed and precision to get the best results.
Materials and Alloys
In die casting, different metals and alloys offer unique benefits. These materials are crucial because they determine the strength, durability, and finish of the final product.
Common Metals Used
Die casting often uses non-ferrous metals such as aluminum, zinc, and magnesium. These metals are popular because they are lightweight and resistant to corrosion.
Aluminum is great for making strong, lightweight parts. It’s often used when you need good thermal and electrical conductivity. Zinc is perfect for smaller components as it allows for precision and detail. It’s highly versatile and easy to mold. Magnesium is the lightest of these metals, providing excellent strength-to-weight ratios, making it ideal for automotive applications.
Other metals like copper, tin, lead, and steel can also be used but are not as common in the die casting process.
Properties of Alloys
Alloys play a significant role in enhancing the properties of metals. They improve factors like strength, resistance to corrosion, and thermal stability. Aluminum alloys are well-known for their ability to resist corrosion and handle temperature changes well. These are ideal for complex, intricate designs that need to withstand harsh environments.
Zinc alloys are preferred when precision is essential. They offer ease of machining and are perfect for detailed parts. Magnesium alloys are chosen for their lightweight properties and are often used in industries where weight is critical, like aerospace.
By selecting the right alloys, you can ensure that your die casting project is both efficient and high in quality.
Design Considerations
When working with die casting, there are several important design factors to consider. These focus on building the mold, ensuring precision and accuracy, and overcoming the challenges of thin-walled designs. Each of these elements plays a crucial role in creating high-quality metal parts with complex shapes.
Mold Construction
Mold construction is a cornerstone of die casting. Tooling for your mold includes the creation of dies that shape the metal. For success, your mold must be robust and designed to withstand high pressures. The die cavity needs to be precisely machined to ensure accuracy.
For complex designs, consider undercuts that can affect mold complexity and cost. Retractable slide cores may solve this issue, allowing for intricate shapes without adding unnecessary expenses. Ensuring the durability and precision of the mold will help maintain part consistency.
Precision and Accuracy
Precision and accuracy are key in die casting. Tolerances dictate the allowable variation in parts, important for consistent quality. Coupling precise tooling with controlled casting conditions helps in achieving repeatable outcomes.
Assembly techniques also impact final accuracy. For instance, threading allows parts to be securely joined using screws, contributing to the part’s functionality and alignment. Keeping tolerances tight ensures the final product meets design specifications, which is vital for industrial applications.
Solving the Challenges of Thin-Walled Designs
Designing with thin walls allows for reduced material usage and lighter parts. Thin-walled designs, however, need special attention. Metal flow must be managed carefully to fill all sections of the mold without causing defects.
Complex geometries can increase difficulty, requiring precise control of temperature and flow rates for success. Balancing these factors helps in solving issues like incomplete filling or warping. By addressing these challenges early in the design process, you can create high-performance parts that meet both durability and efficiency needs.
Die Casting Machines and Equipment
When you’re learning about die casting machines, it’s important to understand two main types: hot chamber and cold chamber machines. Each type has its own unique processes and applications, which impact how materials are injected into molds to create different parts.
Hot Chamber Machines
Hot chamber die casting machines are used mainly for metals with lower melting points, like zinc and magnesium. In these machines, the furnace is integrated with the machine, and the gooseneck component helps to transfer the molten metal into the molds.
The injection process uses a hydraulic press to move the plunger, pushing the metal into the die. This setup results in fast cycle times and high production rates. It’s efficient for manufacturing smaller parts where speed is crucial. The closed system of the hot chamber machine reduces exposure to air, minimizing contamination and oxidation.
Cold Chamber Machines
Cold chamber machines are designed for metals with higher melting points, such as aluminum and copper. Unlike hot chamber machines, the metal is melted in a separate furnace and then transported to the machine in a ladle. The plunger is used to inject the metal into the cylinder and into the mold.
One key advantage is its ability to handle metals that would otherwise cause damage to a hot chamber setup. While it takes longer per cycle, the cold chamber method is ideal for larger parts and is versatile across a wide range of applications. The injection process in these machines is powerful, ensuring detailed and accurate metal parts.
Die Casting Process
Die casting is a highly efficient manufacturing process that shapes molten metal into detailed and accurate parts. Essential elements include preparing the dies, injecting metal under pressure, and finishing the cast products.
Preparing for Production
To start, you need to make sure everything is ready for production. This involves creating a mold or die. The mold is typically made from hardened tool steel and consists of two parts that fit together perfectly.
Producing these molds requires precision because they determine the shape and features of the final product. Before production, these dies are cleaned and coated to ensure a smooth surface finish. This step is crucial to avoid defects.
You also prepare the metal to be used. Depending on the type of die casting, such as gravity die casting or low-pressure die casting, different metals might be chosen, like aluminum or magnesium. The preparation phase sets the stage for a successful casting process and a high production rate.
Injection and Solidification
In this phase, molten metal is injected into the prepared mold. The injection is done under high pressure to ensure that the metal fills all parts of the mold, capturing every detail. Different processes like vacuum die casting or squeeze casting can be used to improve the quality by enhancing strength or reducing air pockets.
Once the metal fills the mold, it begins to cool and solidify. Cooling is controlled carefully to prevent defects like warping. The speed of this phase can impact the production rate, with faster cooling often leading to higher efficiency. The cooling process transforms the molten metal into a solid shape that matches the mold’s design.
Ejection and Finishing
After solidification, the newly formed part is ejected from the die. Ejection must be gentle enough to prevent damage. Once the part is removed, it moves to the finishing stage where any excess material, known as flash, is trimmed away.
Finishing may include polishing to improve surface finish or additional processes to enhance durability. Sometimes, coatings are applied for better appearance or corrosion resistance. Through careful ejection and finishing, the final product meets all the required specifications and is ready for use in various applications. This final touch-up ensures high quality and precision in the parts produced.
Applications and Industries
Die casting is a key process in creating metal parts for many industries. You’re likely interacting with die-cast products every day without even realizing it. Its ability to produce high-quality and precise components is invaluable in sectors like automotive and consumer goods.
Automotive Industry
In the automotive field, die casting is used to create important components like engine blocks and gears. This method supports the mass production of lightweight, strong parts necessary for engines and transmissions. The process is efficient in making accurate and durable pieces, contributing to vehicles’ fuel efficiency.
Die casting helps in producing parts like housings and other metal components. The need for high-volume production makes die casting ideal. You will find that manufacturers rely on its cost-effectiveness for producing bulk amounts with consistent quality.
Consumer Goods and Electronics
For consumer goods and electronics, die casting is crucial. Items like camera bodies, smartphone frames, and small gadgets often rely on this technique. Its precision can produce complex designs, making it perfect for electronics that often have intricate metal casings.
In this area, die casting aids in creating durable, high-quality parts. The process minimizes waste while maintaining strength, which is crucial for consumer products. This efficiency lets manufacturers meet high demand while ensuring the products can withstand everyday use.
Advantages and Considerations
Die casting has various benefits, such as producing strong, precise parts quickly. It also faces certain challenges, but there are solutions to these issues.
Benefits of Die Casting
Die casting excels in creating parts with high strength and dimensional accuracy. The process allows you to make complex shapes with repeatable results, ensuring that each piece meets exact standards. This method is highly efficient, producing large volumes in a short time, which is great for mass production.
Materials used in die casting often offer good corrosion resistance and excellent mechanical properties. With high-density outcomes, components benefit from strong impact strength and a favorable strength-to-weight ratio. Also, alloys used in die casting can provide good thermal and electrical conductivity.
Potential Drawbacks and Solutions
Die casting does have some challenges, such as porosity, which can affect the component’s structural integrity. Porosity is a common issue, but adopting techniques like vacuum die casting can minimize it. Another consideration is initial tooling costs, which can be substantial; however, these costs can be offset by the long-term savings from high-volume production.
Materials may have limitations, affecting dimensional stability and hardness. To tackle these, consider using different alloys tailored to your specific needs. Although die casting is not ideal for all sizes due to high tooling costs, choosing the right project scale can optimize costs and benefits.