API 609 Butterfly Valve Types: Wafer vs lug vs flanged
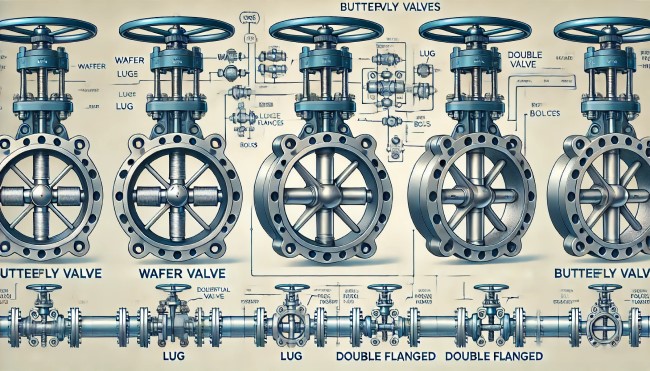
Butterfly valves are industrial devices. They are commonly installed for modulating, controlling, and completely stopping. It allows fluids to flow through pipelines. Butterfly valves have been standardized through the API 609 which sets the limits to the design and performance of the valves. Within the API 609 standard, there are three main types of butterfly valves. The styles include the following; The Wafer and Lug and the Double Flanged. Both types are different in their characteristics and designed for certain uses only. These valve types will be compared in this article and the merits and demerits of each will also be documented.
1. Wafer Butterfly Valve
Of the Wafer butterfly valves, the most preferred and cheapest design is the one used in areas that are limited in space and weight.
Design and Features:
Body Design: Unlike other types of valves, the wafer valve does not include its flanges. However, it is located between two pipe flanges, with the bolts producing contact between the valve body on the one hand and the two adjacent flanges on the other.
Installation: For installation to occur on the pipes, it must hold already flanged ends. Basically on the flanges, the valve is sandwiched and to ensure that it is firmly held in position, there are bolts passed through.
Compact: The design of the wafer is very slim and small in size which provides an advantage where space is a major concern.
Advantages:
Wafer butterfly valves are often easier to manufacture than double flanged valves and, are often cheaper.
Considerations:
Limited Isolation:
A disadvantage of using wafer valves is that they cannot be replaced independently. They may cause problems if standard installation and removal procedures are required.
Requires Flanged Piping:
It can only be adopted where flanged ends are present. Thus restricting its adoption in some systems.API 609 Butterfly Valves play a crucial role in integrity of installation.
2. Lug Butterfly Valve
The Lug butterfly valve is a little more versatile and preferred for systems where shut-off or easy accessibility is desired.
Design and Features:
Lugged Valve Body:
The lug butterfly valve usually has threaded lugs on both sides of the body.
Installation:
Lug valves are easier to fix in the middle of the pipeline line.
Bi-Directional Flow:
Lug valves can thus be used in systems where flow in either direction is required.
Advantages:
Ease of Maintenance:
The lug design enables easier maintenance and replacement.
Versatility:
Due to its design, it serves well the need of maintenance-intensive applications. The valve can be changed out while not interfering with the adjacent pipes. Butterfly Valve Manufacturer makes sure to instill all the features in valves .
Considerations:
Higher Cost:
Lug valves cost relatively higher than wafer valves because of the extra design and construction aspects integrated into the type.
Bulkier: These valves are generally a bit larger and heavier, thus, may not be suited for where space is a limiting factor.
3. Double Flanged Butterfly Valve
The double-flanged butterfly valve is the largest of the three, with a stronger and more secure connection with more pressure handling ability.
Design and Features:
Dual Flanges: This valve has flanges on either end of the valve body that are screwed onto the pipes as shown below. The double flanged design is more effective than that of a wafer or lug valve for this application.
Installation: It is attached by clamping which screws directly into the pipeline at the entrance and exit, which gives a strong and vice-free connection.
Heavy-Duty: Two-weld neck valves are meant for use in applications that exert pressure on the valve bodies and big diameter pipes in particular day.
Advantages:
Durability:
There are two basic types of valves, the double flanged valves fit high pressure and high volume application such as industrial usage.
Secure Connections:
The two flanges provide a reliable seal, which is necessary in the zones of high pressure or when the working substance is hazardous.
Considerations:
Cost and Complexity:
Double flanged valves are the most costly; they use bolts and flanged connections more than wafer or lug valves and so have the longest install time.
Space Requirements:
These valves are larger in size and need more space, and thus can be a constraint in some kinds of applications.
Conclusion
Depending on the demands of the application, standard Wafer, Lug or Double Flanged butterfly valves can be used. The features of the design of these valves are that they are relatively cheap and are suitable where piping is to be prefabricated with flanges. Lug valves may be fixed in any position with reference to flow. And on-off or throttling tasks; these types of valves can be removed without affecting the pipes. Hence appropriate for bi-directional flow jobs.
With the various types of butterfly valves, design, installation, and operation, it becomes easy to choose the most appropriate valve type for your system.