Maximizing Efficiency in Ultrasonic Welding Processes
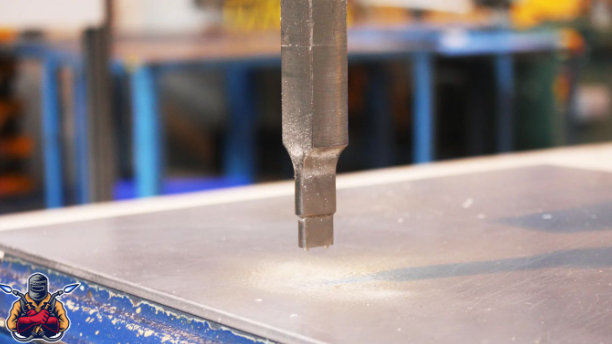
Ultrasonic welding is an exceptionally effective method utilized in different businesses, from gadgets to car and clinical gadget producing. This cycle utilizes high-recurrence ultrasonic vibrations to join materials, regularly plastics or metals, without requiring weld, cements, or latches. The productivity of ultrasonic welding relies upon a few elements, including machine settings, material properties, and functional practices. In this article, we will investigate ways of amplifying effectiveness in ultrasonic welding processes, zeroing in on streamlining the utilization of a ultrasonic welder and understanding the job of the wire bonder.
Key Elements in Ultrasonic Welding Proficiency
Legitimate Machine Arrangement
The proficiency of ultrasonic welding starts with right machine arrangement. The ultrasonic welder should be aligned by the particular materials being welded. Changing boundaries like recurrence, plentifulness, and welding pressure is urgent for accomplishing steady areas of strength for and. Utilizing the right recurrence (normally between 20 kHz and 40 kHz) can assist with guaranteeing that the vibrations are upgraded for the material properties, lessening energy utilization and expanding efficiency.
Material Similarity
Understanding the materials engaged with the welding system is fundamental. The similarity of the materials being joined influences the strength and nature of the weld. Plastics, for instance, should have comparative softening focuses for the best holding results. In metals, ultrasonic welding works best when the surfaces are spotless and liberated from impurities, for example, oil or oxidation, that could obstruct the security.
Improving Welding
Time Lessening welding time without compromising weld quality is critical to augmenting effectiveness. This can be accomplished by refining the power input and changing the power applied during welding. More limited welding times mean quicker creation cycles, yet they should be painstakingly controlled to stay away from feeble welds or harm to the parts. Numerous makers enhance welding time by directing tests with different machine settings until the ideal harmony between time and strength is found.
Utilizing Great
Tooling, including the horn and iron block, assumes a basic part in the ultrasonic welding process. The horn sends the ultrasonic vibrations to the materials, and its plan should match the state of the parts being welded. Excellent tooling lessens mileage on the gear, limiting personal time for support and substitution. Customary investigation and cleaning of tooling parts can likewise forestall weld irregularities, guaranteeing reliable result.
Observing and Robotization
Numerous cutting edge ultrasonic welders come outfitted with cutting edge checking frameworks and mechanization abilities. Observing boundaries like welding energy, time, and plentifulness can assist administrators with fining tune the interaction for higher proficiency. Robotization can likewise further develop accuracy and lessen administrator mistake. Robotized frameworks guarantee repeatability, which is essential for high-volume creation conditions where consistency is urgent.
Wire Bonder Reconciliation
In applications where fine electrical associations are required, for example, in semiconductor bundling or microelectronics, a wire bonder is frequently coordinated into the ultrasonic welding process. Wire holding is a strategy used to make electrical interconnections by welding slight wires, commonly gold or aluminum, onto cushions or terminals. Guaranteeing that the wire bonder is very much adjusted and synchronized with the ultrasonic welding process keeps an elevated degree of accuracy and productivity, particularly in delicate applications.
Energy Effectiveness
Ultrasonic welding is for the most part an energy-proficient cycle, however there are ways of advancing streamline energy utilization. Legitimate upkeep of the welder, including supplanting worn parts and guaranteeing that the power supply is steady, can forestall pointless power floods. Furthermore, utilizing welders that offer customizable power settings permits administrators to coordinate the energy input with the material prerequisites, diminishing energy squander.
Best Practices for Amplifying Ultrasonic Welding Effectiveness
Preparing and Talented Administrators
Administrators should be thoroughly prepared in the activity of ultrasonic welders and wire bonders. Appropriate preparation guarantees that machines are set up accurately, and administrators can rapidly distinguish and address any issues that emerge during the welding system.
Normal Support
Planned upkeep keeps an eye on ultrasonic welding machines guarantee they work at top effectiveness. Precaution support decreases margin time and the requirement for expensive fixes or substitutions.
Information Driven Improvement
Use information from observing frameworks to follow the presentation of the ultrasonic welder. This information can assist with recognizing patterns, for example, when weld quality disintegrates, taking into account precautionary acclimations to the cycle.
Material Testing
Direct normal tests on the materials utilized in welding to guarantee they are reliable in quality. Conflicting material properties can prompt varieties in weld strength, requiring more regular acclimations to the welding system.
FAQs
What is ultrasonic welding?
Ultrasonic welding is a cycle that utilizes high-recurrence sound waves to bond materials together. It is usually used to join plastics and metals without the requirement for glues, clasp, or intensity.
How does a ultrasonic welder function?
A ultrasonic welder utilizes high-recurrence vibrations to make grinding between materials, producing restricted heat that melts and bonds them. The interaction is fast and exact, making it ideal for different modern applications.
What is a wire bonder, and how can it connect with ultrasonic welding?
A wire bonder is a machine used to make fine electrical associations in electronic gadgets by welding slim wires onto parts. Now and again, wire holding is coordinated with ultrasonic welding, particularly in microelectronics fabricating, to guarantee secure and proficient associations.