Why Preventative Maintenance is a Business Must-Have in 2025
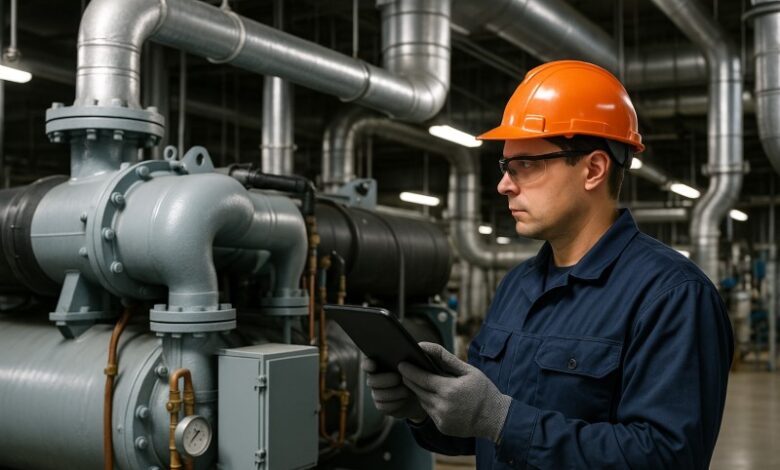
For industries that rely on stable temperature control, such as plastics, automotive, food and beverage, and general manufacturing, the risk of downtime is amplified. A single faulty chiller can compromise product quality, create safety risks, and trigger costly delays. Despite this, many businesses still adopt a reactive approach to maintenance — dealing with problems only after they occur. In 2025, this simply isn’t sustainable.
Downtime Isn’t Just Disruptive — It’s Expensive
The true cost of downtime is often underestimated. Lost productivity, missed deadlines, and product spoilage can result in losses running into thousands — or even millions — of pounds. For facilities that operate around the clock, like data centres or food processing plants, every hour offline is measurable in real financial terms.
In a study by Siemens, it was estimated that downtime costs manufacturers in the UK an average of £180,000 per hour. While this figure may vary across industries, the underlying message is clear: Equipment failure is a serious business risk. This is especially true for systems that don’t typically receive day-to-day attention, such as chiller units, heat pumps, or recirculating cooling systems. When they fail, the consequences can be both sudden and far-reaching.
Why Reactive Maintenance No Longer Works
Traditionally, many businesses have relied on reactive maintenance. That is, waiting for something to break, then fixing it. While this approach may seem cost-effective in the short term, it creates several long-term vulnerabilities.
First, it offers no opportunity for forward planning. When a breakdown occurs unexpectedly, it often leads to emergency callouts, out-of-hours repair rates, and limited parts availability. Second, reactive maintenance can contribute to repeat issues, particularly if the underlying causes — such as poor airflow, scaling, or refrigerant leaks — aren’t properly addressed.
Finally, there’s the issue of compliance. Businesses in sectors like food and beverage or pharmaceuticals are bound by strict regulations regarding temperature control, cleanliness, and equipment reliability. A failed cooling unit might not only halt production and require emergency chiller repairs but also lead to product recalls or regulatory fines.
The Business Case for Preventative Maintenance
Preventative maintenance is the strategic alternative. Rather than waiting for something to go wrong, it focuses on regular inspections, servicing, and component replacements based on usage and performance data. This approach helps businesses identify potential issues before they develop into larger problems.
For example, industrial chiller maintenance might involve checking refrigerant levels, inspecting for leaks, descaling heat exchangers, cleaning condenser coils, and verifying pressure readings. These tasks, though relatively simple, can dramatically improve system reliability and efficiency.
One of the greatest benefits of preventative servicing is predictability. With planned maintenance schedules in place, businesses can budget more accurately, reduce emergency callout fees, and avoid the costly impact of unexpected breakdowns. Over time, this results in a longer equipment lifespan and improved return on investment.
The Impact on Sustainability and Energy Costs
Another strong argument for preventative maintenance is its contribution to energy efficiency. Industrial cooling systems are major energy consumers. When they’re not working properly — for example, if filters are clogged or refrigerant levels are off — they have to work harder to maintain the desired temperature. This results in increased energy use, higher bills, and unnecessary emissions.
In the current climate, where businesses are under pressure to meet sustainability targets and reduce carbon output, neglected cooling systems can become an unexpected source of waste. By contrast, a well-maintained unit operates more efficiently, consumes less energy, and aligns more easily with ESG policies and reporting requirements.
Maintenance isn’t just about avoiding breakdowns — it’s also about performance. A system running at 80% capacity due to blocked airflow or sediment build-up may still be working, but it’s not delivering value. With energy prices still volatile, optimising cooling performance is a smart way to take control of operational expenses.
Tailored Maintenance Agreements: A Strategic Asset
One of the most effective ways to manage preventative maintenance is through a service agreement tailored to the business’s specific needs. This could involve quarterly inspections, annual overhauls, emergency response callouts, or 24/7 cover depending on the risk profile.
Industrial and commercial environments often have very different cooling requirements. A plastic injection moulding plant, for instance, might need rapid temperature changes and constant uptime, while a logistics company may only require seasonal support for warehouse cooling. Having a maintenance partner that understands these nuances is essential.
Working with a specialist provider of industrial chiller maintenance can offer peace of mind that systems are being handled by engineers familiar with the equipment type, industry regulations, and brand-specific servicing procedures. This is especially important when dealing with older or legacy systems, where improper maintenance can accelerate wear and reduce reliability.
Final Thoughts
In 2025, unplanned downtime is more than just an inconvenience — it’s a measurable business liability. From product spoilage to missed contracts and rising energy costs, the financial risks are too significant to ignore.
That’s why forward-thinking businesses are shifting their approach. By prioritising preventative chiller maintenance and investing in smart service partnerships, they’re not only protecting their assets but also gaining a competitive edge. Whether you’re managing a manufacturing site, operating a fleet of commercial buildings, or running a critical facility like a data centre, the message is clear: look after your cooling systems, and they’ll look after your bottom line.