How Does Industrial X-ray Inspection Detect Defects in Materials?
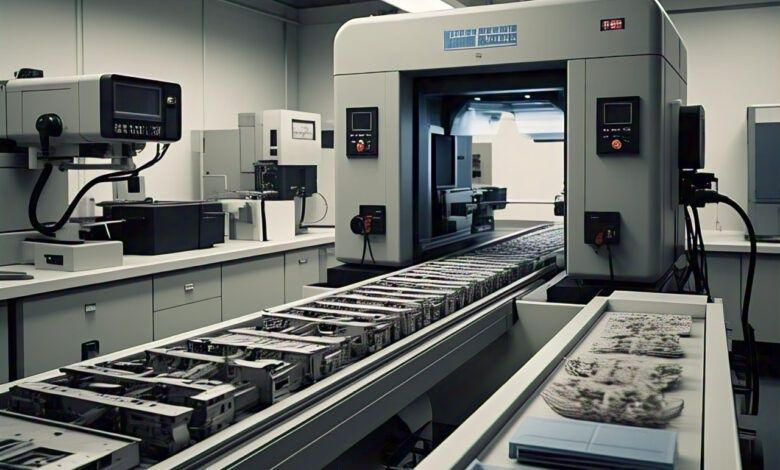
Industrial X-ray inspection is a critical non-destructive testing (NDT) technique used across various industries to ensure product quality, safety, and reliability. It provides manufacturers with the ability to detect hidden defects in materials without damaging the components being inspected. This advanced imaging technology plays a vital role in identifying structural flaws, inconsistencies, and internal defects that may compromise product integrity.
What is Industrial X-ray Inspection?
Industrial X-ray inspections, also known as radiographic testing (RT), utilizes high-energy X-rays or gamma rays to penetrate materials and create detailed images of their internal structures. This allows manufacturers to examine components for defects such as cracks, voids, porosity, misalignments, and foreign inclusions that would otherwise be invisible to the naked eye.
The process involves:
- X-ray Generation: An X-ray tube or radioactive source emits high-energy radiation.
- Material Penetration: The X-rays pass through the material being inspected.
- Image Capture: A detector or film captures the transmitted rays, creating an image based on material density variations.
- Defect Identification: Specialists analyze the resulting radiographs to identify irregularities and potential defects.
Types of Defects Detected by Industrial X-ray Inspection
Industrial X-ray inspection is highly effective in identifying a wide range of material defects, including:
1. Cracks and Fractures
Internal or external cracks, often caused by stress, fatigue, or improper manufacturing processes, can compromise structural integrity. X-ray imaging reveals these fractures before they lead to part failure.
2. Porosity and Voids
Tiny air pockets or voids within castings, welds, and molded components can reduce strength and durability. X-ray inspection identifies these inconsistencies to help manufacturers refine their production techniques.
3. Inclusions and Foreign Materials
Undesirable particles or materials embedded within a component can affect functionality and quality. X-ray imaging detects these inclusions, ensuring material purity and performance.
4. Weld Defects
Welded joints are critical in many industries, and defects such as incomplete fusion, slag inclusions, or lack of penetration can weaken structures. X-ray inspection provides a detailed view of weld integrity.
5. Wall Thickness Variations
Uneven wall thickness in pipes, tubes, and other components can lead to premature wear or failure. X-ray inspection helps ensure uniform thickness and material consistency.
6. Hidden Assembly Issues
In complex assemblies, misaligned or missing components can cause mechanical failures. X-ray inspection verifies internal structures without disassembling the product.
Benefits of Industrial X-ray Inspection
1. Non-Destructive and Highly Accurate
Unlike destructive testing methods, X-ray inspection allows manufacturers to examine components without damaging them, preserving the integrity of tested products.
2. Fast and Efficient Quality Control
X-ray inspection is a quick process that helps manufacturers identify defects in real-time, reducing production downtime and minimizing waste.
3. Cost Savings and Waste Reduction
By detecting defects early in the manufacturing process, companies can avoid costly recalls, reduce material waste, and improve overall efficiency.
4. Enhanced Safety and Compliance
Industries such as aerospace, automotive, and medical devices require strict quality assurance. X-ray inspection ensures compliance with safety regulations and industry standards.
5. Improved Product Longevity and Performance
Detecting defects before products reach consumers ensures reliability and extends product lifespan, enhancing brand reputation and customer satisfaction.
Industries That Benefit from Industrial X-ray Inspection
- Aerospace: Ensuring defect-free aircraft components for safety and durability.
- Automotive: Inspecting engine parts, welds, and castings for quality assurance.
- Medical Devices: Verifying the integrity of implants, surgical tools, and electronic components.
- Electronics: Detecting solder joint defects and internal circuitry issues in PCBs.
- Oil and Gas: Checking pipeline integrity and weld quality for safety compliance.
- Additive Manufacturing (3D Printing): Ensuring consistency and structural soundness of printed components.
Conclusion
Industrial X-ray inspection is an invaluable tool for detecting hidden defects in materials, ensuring product safety, and optimizing manufacturing processes. By providing non-destructive, high-resolution imaging, it enhances quality control, reduces costs, and supports regulatory compliance across various industries. As manufacturing continues to evolve, X-ray inspection remains a crucial technology for maintaining high standards in product reliability and performance.